- Lab Manager Academy
- Subscribe Today!

Slippery Business
Creating the best slip, trip, and fall prevention program for your lab.
Vince McLeod is an American Board of Industrial Hygiene-certified industrial hygienist and the senior industrial hygienist with Ascend Environmental + Health Hygiene LLC in Winter Garden, Florida. He has more...
Again and again we hear about the dangers of slips, trips, and falls and the heavy cost associated with the resulting injuries. A few recent statistics hammer home the reality of the concern:
1. Slips and falls account for 12 percent of all work related deaths.
2. fatal injuries in slips and falls rank second behind motor vehicle deaths in the workplace., 3. slips and falls cause more than 300,000 disabling injuries and deaths annually., 4. costs in compensation (wages and medical) as a result of slipping accidents average $6,717 per occurrence (more than 41 percent above the average of all other accidents)., 5. work-related accidents in the united states cost $34.8 billion annually. 1.
And you may not think so, but laboratory facilities are prime candidates for slips and falls. The constantly wet surfaces, frequent spills and splashes, constant washing of glassware, etc., all combine to make laboratories some of the places most vulnerable to slips, trips, and falls. So in this issue, the Safety Guys offer a few tips on preventing these types of accidents
Look at the big picture
There are many reasons for slips and falls, but they have one thing in common—they usually could and should have been prevented. Accidents do happen; however, by using a commonsense approach and following some simple key steps we can avoid the major causes of slips and falls. As in other safety programs, employee participation and vigilance are key to success. This is especially important with trips, slips, and falls, as the hazards are dynamic (i.e., constantly changing), so it is imperative that employees observe and take preventive action during their day-to-day activities.
The first thing to do is to take the time to survey your facility and try to identify potential problem areas. Once these trouble zones are spotted, you then can evaluate fixes or different control measures. Finally, implement the corrections and controls. After addressing the trouble areas, it is a simple matter to perform a facility inspection at regular intervals, maintaining, repairing, and replacing controls as needed.
We know from experience that rough, dry concrete sidewalks have good traction and that icy, wet, or smooth surfaces often do not. The technical term for this is coefficient of friction (COF). The higher the COF, the more traction that surface offers. Field measurement of COF is difficult and often inaccurate. The COFs mentioned are from lab data on dry surfaces. For most walking and working surfaces, we should aim for a COF of 0.40 or greater for the best traction. As a reference, a dry, rough concrete sidewalk may have a COF of 1.0 or more, while a wet, smooth surface such as ceramic tile or ice can have a COF of as low as 0.10. Let us keep that in mind as we begin our survey.
Take a walk on the outside
Start by taking a tour outside, walking around the perimeter of your research facility. Make a list of the usual suspects when it comes to areas where trips and falls occur most frequently. These include entrances, sidewalks, steps, and ramps. Take note of the different surfaces and whether they have good traction. We suggest trying the “scuff test” of sliding or kicking your foot along the surface in both dry and wet conditions. If the surface seems slippery, then it is a good candidate for nonskid epoxy coatings or nonslip treads. Areas that are very frequently used in locales with wet weather should also be considered for permanent coverings to reduce slipping.
Are the usual suspects likely to get wet at times other than in inclement weather? For example, does the irrigation system or do sprinklers hit these potential trouble spots? If so, have them corrected immediately. Does their proximity to water, such as from roof drains or storm water systems, lead to regular wetting? Then nonskid coatings with a very high COF are a must.
Do not overlook shipping and receiving areas or loading docks. These high-traffic areas are often exposed and must have excellent traction due to the added hazards of moving loads in and out. Also, make sure all steps, ramps, and elevated docks have appropriate guardrails.
Another hazard to look for is uneven surfaces. Very small changes in elevation can lead to a trip from a “stubbed” toe, resulting in a fall. In fact, the Americans with Disabilities Act (ADA) requires differences in elevation to be a quarter-inch or less.2 The best fix is to fill in or grind down the adjacent areas to smooth them out. If that is not practical, consider yellow safety markings to draw attention to the change in levels.
Since most research facilities do not adhere to a strict 8-to-5 workday and activities can take place before and after daylight hours, make sure you visit your trouble spots in the dark in order to evaluate the lighting. It is very helpful and recommended that a good-quality light meter be used for this survey, and that the results be compared to the national consensus standards.
Inside track
Continuing our inspection indoors, we encounter a variety of uses, each with different requirements. Typically we have offices; break rooms, canteens, and perhaps cafeterias; receiving and storage areas; workshops; and, of course, laboratories. The floor surfaces and the hazards vary with the intended use of each space.
Housekeeping issues are the number one reason for trips and falls indoors. Therefore, avoiding clutter and keeping floors and walkways clear are important for all areas. Check for stray or inappropriate cords, such as extension cords and computer or phone cables, and reroute them properly if they are present. Ensure that mats lie flat, and secure them if they tend to move. Repair any bulges in the carpets, and take extra care where floor surfaces change— for example, where carpet meets tile or other flooring—to keep them smooth and trip-free.
Receiving and storage areas and workshops present special challenges and need a nonslip floor with a high COF. It is a good idea to designate paths and walkways with on-floor markings to aid in keeping these areas clear.
Any specific washing areas or tank rooms need special attention. It is highly recommended that walking and working surfaces in these areas have nonskid coatings, due to their frequently wet conditions. Use anti-fatigue mats wherever employees must stand for long periods. Make sure employees know to clean up any spills immediately. In addition, expanding your lighting survey to indoor areas is another recommended prevention task.
Taking a few hours to inspect your research facility will go a long way in preventing slips, trips, and falls. Most fixes and corrections are low-cost and easily installed and maintained. Given the costs associated with the alternatives, it is hard to argue against a good slip, trip, and fall prevention program.

Slip, Trip, and Fall Prevention for Healthcare Workers
December 2010, dhhs (niosh) publication number 2011-123.

According to the U.S. Bureau of Labor Statistics [2009], the incidence rate of lost-workday injuries from slips, trips, and falls (STFs) on the same level in hospitals was 38.2 per 10,000 employees, which was 90% greater than the average rate for all other private industries combined (20.1 per 10,000 employees). STFs as a whole are the second most common cause of lost-workday injuries in hospitals.
Slip, Trip, and Fall Prevention for Healthcare Workers pdf icon [PDF 979.73KB]
Follow NIOSH
Niosh homepage.
- Workplace Safety & Health Topics
- Publications and Products
- Contact NIOSH
Exit Notification / Disclaimer Policy
- The Centers for Disease Control and Prevention (CDC) cannot attest to the accuracy of a non-federal website.
- Linking to a non-federal website does not constitute an endorsement by CDC or any of its employees of the sponsors or the information and products presented on the website.
- You will be subject to the destination website's privacy policy when you follow the link.
- CDC is not responsible for Section 508 compliance (accessibility) on other federal or private website.
Slips, trips and falls in the workplace
Walking with your hands full, responding to a text while crossing the parking lot or working with a mess on the floor—each of these seemingly small distractions are actually serious workplace hazards. In June, safety trainings will cover slip, trip and fall prevention at Sanford Underground Research Facility (Sanford Lab).
“Slips, trips and falls are a primary cause of work-related injuries,” said Larry Jaudon, director of Sanford Lab’s Environment, Safety and Health Department. “At Sanford Underground Research Facility, we take a proactive approach to providing a safe and healthy work environment for our team.”
The Occupational Safety & Health Administration (OSHA) has identified that slips, trips and falls are responsible for 15% of all accidental deaths; second only to motor vehicle related incidents. In addition to the unnecessary pain and suffering which results from a fall; the National Safety Council reports that slips, trips and falls cost society over 13 billion dollars a year and are the second leading cause of disabling workplace injuries. In general industry, the average cost of a slip, trip or fall, is approximately $40,000.00 per incident.
“We have recently updated our fall protection and fall prevention requirements and will retrain all SDSTA personnel in the requirements of these standards starting in June,” said Jaudon. “Additionally, we have provided for annual refresher training in this subject for all our employees.”
SURF continues to be at the forefront of hazard awareness, ensuring that our personnel are adequately trained and provided with the best possible equipment to protect them from risks associated with slips, trips and falls.
The Environment, Safety and Health Department at Sanford Underground Research Facility promotes health and safety in the workplace, as well as healthy living and wellness for all employees. If you have questions about health and wellness, please contact our occupational health nurse, Laura Baatz, who is onsite daily at [email protected] .
SafeStart solves your biggest challenges - from slips, trips and falls to serious injuries and fatalities - by addressing the human factors common to all of them.
Capabilities.
Discover human factors management solutions that effectively address human error, conquer common injury challenges and improve safety engagement.
- Rate Your State
Organization
- Safety Assessment & Diagnostics
- Human Factors Review
Our safety resources give you the knowledge and stories you need to manage human factors—and won’t find anywhere else.
Safety Resources
Customer success.
- Case Studies
- Video Testimonials
Let us show you how to connect the dots between human error reduction and fewer incidents, better engagement and stronger support for safety.
Workshops & Events
- Event Calendar & Map
- SafeStart Forum
Please select your region
Por favor elige tu región Veuillez choisir votre région Per favore scegli la tua regione Por favor escolha a sua região Bitte wählen Sie Ihre Region aus
USA & Canada
- USA & Canada (English)
- Canada (Français)
Latin America
- America latina (Español)
- Brasil (Português)
- International (English)
- France (Français)
- Deutschland (Deutsch)
- Italia (Italiano)
- España (Español)
- UK (English)
- Asia (English)
Blog / May 16, 2016
3 Big Causes of Slips, Trips and Falls
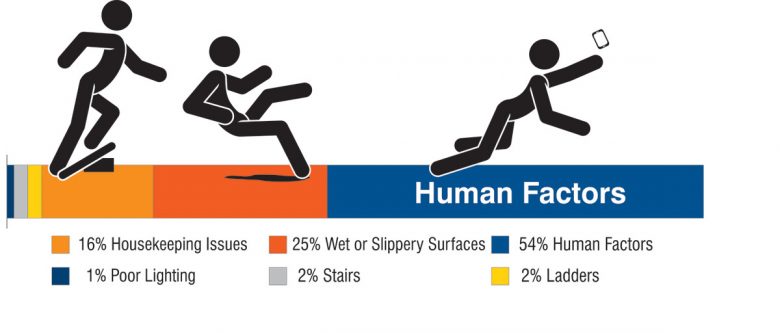
This is an excerpt from our free guide on preventing slips, trips and falls .
A 2014 survey of 1,294 safety professionals revealed the most frequent factors in slip, trip and fall incidents at their workplaces—and a whopping 95% of respondents cited one of three causes.
The main characteristic the three biggest causes have in common is they’re the result of the errors or errors in judgement that people make every day, like how tidy to keep their work area, whether to report a wet surface or debris that could be a trip hazard, how fast to walk, and whether to move blindly around corners. People tend to perceive these hazards (and especially human factors) as being a lot less risky than they actually are, which makes it challenging to find effective and permanent solutions.
Because these factors require constant attention, they can be avoided entirely (or made worse) by employees’ mental states throughout the day.
One step at a time
Most safety programs focus on the physical hazards of slips, trips and falls, like the conditions of commonly used areas such as a well-traveled walking surface, stairway or ladder. Fall hazards should always be your first priority, but you can’t eliminate injuries caused by slips, trips and falls by only dealing with physical factors.
The truth is that many slips, trips and falls are caused or made worse by a person’s state of mind. When we’re rushing, frustrated, tired or complacent we tend to make errors and decisions that increase the chance of injury.
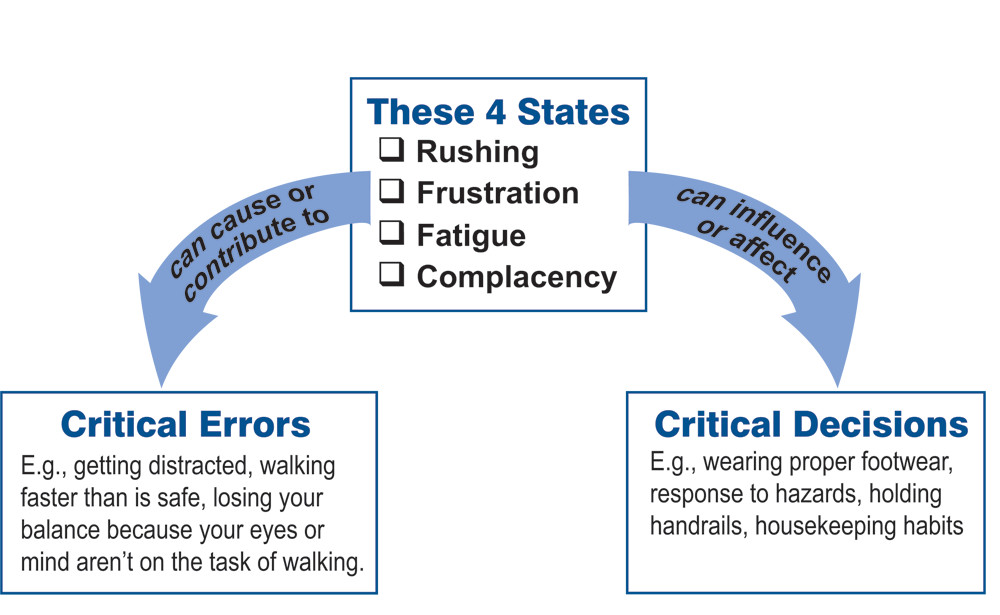
Nobody chooses to slip and fall. But no matter how effective the rest of your safety program is, your employees have a higher risk of injury due to a slip, trip or fall when they’re in one of these four states.
If you’ve done everything you can to minimize physicals hazards, your next step in preventing slips, trips and falls is clear: you need to address human factors.
Discover how to address human factors in your slips, trips and falls prevention efforts by downloading Solving Slips, Trips and Falls Once and For All: A guide to addressing the physical and human factors in slips, trips and falls for free.
Slips, Trips and Falls Guide
What You Don’t Know about Same-level Falls
Discover the major physical and human factors involved in slips, trips and falls—and practical solutions to prevent incidents.
Tagged Slips Trips and Falls

EHS Daily Advisor
Practical EHS Tips, News & Advice. Updated Daily.
Back to Basics, Injuries and Illness
Back to basics: slips, trips, and falls.
Updated: Oct 23, 2023
Back to Basics is a weekly feature that highlights important but possibly overlooked information that any EHS professional should know. This week, we examine slips, trips, and falls.
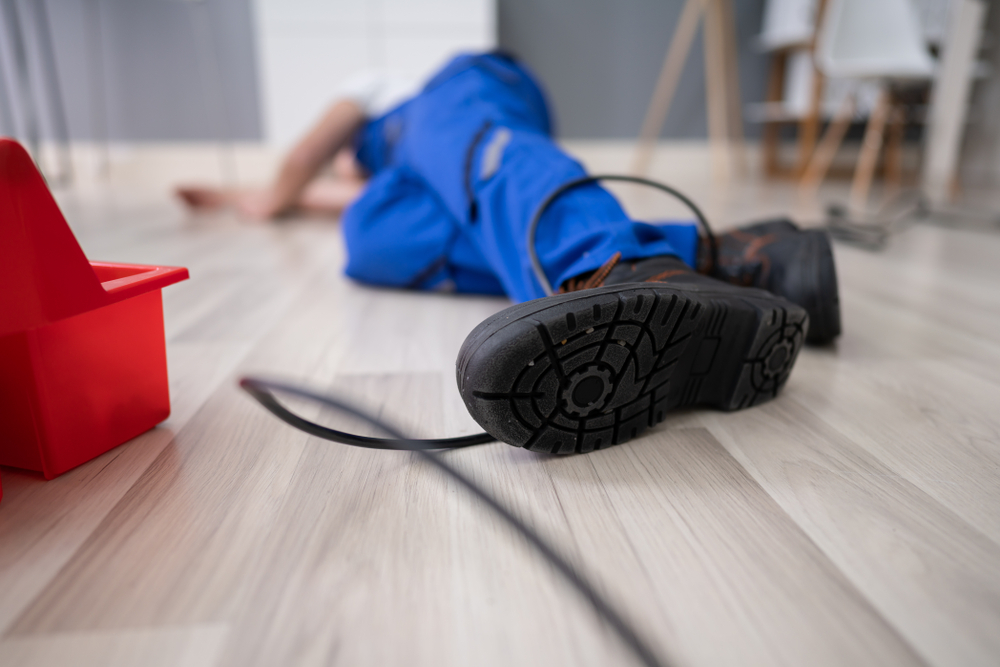
How much are workplace slips, trips, and falls costing you?
“Falls on the same level” often get lumped together with falls from height in slips, trips, and falls. While falls from height can sometimes be fatal, falls on the same level can lead to costly nonfatal injuries, resulting in several days away from work for injured workers and workers’ compensation claims for employers.
According to insurer Liberty Mutual, falls on the same level cost employers $8.98 billion a year. Falls on the same level are the second-leading cause of seriously disabling workplace injuries in the insurer’s 2023 Liberty Mutual Workplace Safety Index .
“Overexertion involving outside sources,” or lifting heavy objects, is the index’s leading cause of disabling injuries.
“Slip or trip without fall” is the ninth leading cause of disabling injury, according to Liberty Mutual’s index. Liberty Mutual reported that injuries on slippery or uneven walkways cost employers $1.98 billion a year.
First, some definitions: Slips are a loss of balance directly caused by too little friction between workers’ feet and walking surfaces. Wet surfaces, spills, and weather hazards like ice and snow can lead to a lack of friction.
Trips occur when workers’ feet hit an object and workers are moving with enough momentum to be thrown off balance.
Falls on the same level occur when workers get too far off their center of balance.
Safety professionals aware of slip, trip, fall hazards
Travelers, another insurer, reported that slips, trips, and falls on the same level are the second-leading cause of injury, accounting for 15% of all accidents, with approximately 25,000 slip, trip, and fall accidents occurring daily in the United States.
According to the National Safety Council (NSC), falls on the same level are the third-leading type of preventable injury at work after exposure to harmful substances and overexertion injuries. Falls on the same level affect every industry and workplace but are prevalent in the service, healthcare, and retail industries, according to the NSC.
Data shows that the median number of days away from work following a fall on the same level is 12 days.
The NSC suggests that effective signage can help prevent injuries, regulatory violations, and higher insurance premiums.
Slip, trip, and fall hazards show up in many industries, but wholesale and retail trade (WRT) establishments suffer high rates of slip, trip, and fall injuries. The National Institute for Occupational Safety and Health (NIOSH) offered several recommendations for protecting workers in the wholesale and retail industries.
Hazardous workplace factors include boxes or containers that obstruct workers’ field of vision; ice, rain, and snow; loose mats or rugs; poor lighting; spills that can create slippery surfaces; and walking surfaces that are in disrepair, have protruding nails and boards, or have changes in floor height.
NIOSH’s recommendations for employers include the following:
- Develop a written slip, trip, and fall prevention policy that spells out both employer and worker responsibilities.
- Ensure that aisles and passageways are free of clutter and other tripping hazards.
- Provide proper lighting in all areas indoors and outdoors to reduce shadows, dark areas, and glare so that trip hazards or surface irregularities are clearly visible, and promptly replace burnt-out light bulbs.
- If electrical cords are regularly used in a workspace, install outlets so that cords don’t cross walkways.
- Select flooring material according to the work performed in an area.
- Provide cleanup supplies—paper towels, absorbent material, “wet floor” signs, etc.—at convenient locations in the facility.
- Provide umbrella bags to prevent rainwater from dripping onto the floor.
- Use mats to provide slip-resistant walking surfaces by absorbing liquid and removing dirt, debris, and liquid from shoes. Mats should be large enough so that several footsteps fall on the mat and clean contaminants off the shoes.
- Provide water-absorbent mats near entrances and other areas where water, ice, or snow may drip or be tracked onto the floor.
- In grocery stores, ensure water from produce spray misters is directed onto produce and not spraying onto the floor.
- In grocery stores, provide customers with paper towels and plastic bags and for wet produce to prevent it from dripping water onto the floor.
You should supplement engineering controls with worker training. You need to train employees to identify slip, trip, and fall hazards and how to prevent slips, trips, and falls by using safe cleaning procedures and placing caution signs and/or cones around the site to warn other employees and visitors to avoid wet walking surfaces.
NIOSH also has employer guidance for preventing slips, trips, and falls in health care. According to NIOSH, the top slip, trip, and fall hazards in health care are:
- Contaminants (fluids, food, grease, oil, and water) on the floor;
- Poor drainage of drains and pipes;
- Walking surface irregularities indoors and outdoors like uneven flooring or ground and holes, protrusions, and rocks;
- Weather conditions like ice and snow;
- Inadequate lighting;
- Stairs and handrails;
- Stepstools and ladders;
- Tripping hazards like clutter, loose cords, hoses, wires, and medical tubing; and
- Improper use of floor mats and runners.
NIOSH’s guide includes an extensive checklist of slip, trip, and fall hazards that should be addressed in a healthcare facility.
OSHA has its own checklist for recognizing slip, trip, and fall hazards in the workplace. The list covers the general work environment, as well as aisles and walkways; escalators; elevated surfaces; floor and wall openings; ladders and scaffolding; parking lots and sidewalks; and ramps, stairs, and stairways.
NIOSH also warns young retail workers that slips, trips, and falls can result in bruises, bumps, cuts, fractures, scratches, sprains, and strains. The institute cautions young workers to clear stairs and walkways of tripping hazards like cords and wires, clutter, and empty cartons; to use handrails when walking up and downstairs; and to clean up spills and anything slippery on floors and the rungs, steps, and feet of ladders.
Control measures and training can be further supplemented with personal protective equipment. Employees who work on wet or contaminated walking surfaces should wear slip-resistant shoes. Workers should choose footwear that’s also resistant to chemicals, heat, and oil.
NIOSH has looked into the value of wearing slip-resistant shoes.
Laboratory studies of slip-resistant footwear to reduce slips, trips, and falls had shown promise in reducing slips, but until a few years ago, there was little research showing the effectiveness of slip-resistant shoes.
In 2019, NIOSH researched the effectiveness of slip-resistant shoes in a study of 17,000 food service workers in 226 school districts serving kindergarten through 12th-grade students. Workers were randomly assigned either to a group that received no-cost, “5-star-rated” slip-resistant shoes or to a group that bought their own slip-resistant shoes.
Researchers looked at workers’ compensation injury claims for accidents caused by slipping on wet or greasy surfaces to evaluate the effectiveness of the shoes.
The group that was provided with highly rated slip-resistant shoes saw a 67% reduction in claims for slip injuries.
There was a baseline of 3.54 slipping injuries per 10,000 months worked among the intervention group, which was reduced to 1.18 slipping injuries per 10,000 months worked after slip-resistant shoes were provided.
Employees who handle materials should ensure the walkways are unobstructed before transporting large materials that might block their view. They should walk with caution and make wide turns at corners. They also should push rather than pull carts to allow a better line of sight.
Housekeeping measures can also help prevent slips, trips, and falls. Your housekeeping policies should include:
- Cleaning floors and work surfaces as soon as they become wet;
- Inspecting refrigerated and freezer cases for water leakage onto the floor surfaces and placing absorbent strips and water-absorbent mats on the floor until the unit is repaired;
- Placing warning signs in wet-floor areas and removing them promptly when floors are clean and dry;
- Using no-skid waxes in slippery areas and using soap that doesn’t leave a slippery residue;
- Maintaining drainage and providing false floors (elevated floors usually 2 to 4 inches above the structural floor designed to provide a surface for safe transit), platforms, or nonslip mats during wet or oily processes;
- Cleaning only one side of a passageway at a time to allow room for passing;
- Keeping passageways clear at all times and marking permanent aisles and passageways; and
- Taping or anchoring electrical cords to floors if they cross walkways.
Workplace housekeeping
In a safety talk handout , the NSC emphasizes the importance of workplace housekeeping in factories and manufacturing plants, offices, and warehouses.
Workplace housekeeping can prevent slip, trip, and fall hazards, as well as control fire hazards and prevent falling objects.
The NSC recommends housekeeping measures suggested by the Canadian Centre for Occupational Safety and Health (CCOSH) that include:
- Cleaning all spills immediately;
- Mopping or sweeping debris from floors;
- Marking spills and wet areas;
- Removing obstacles from walkways and keeping walkways free of clutter;
- Securing carpets, mats, and rugs that don’t lay flat (tacking or taping floor coverings, for example);
- Ensuring file cabinet or storage drawers are closed;
- Covering cables or cords that cross walkways; and
- Keeping working areas and walkways well lit and replacing used light bulbs and faulty light switches.
Some industry groups tout “how to fall” training as a method of mitigating slip, trip, and fall injuries. Others offer “safe walking” tips like “watch where you are going,” “be aware of your environment,” “keep an eye out for changes in elevation,” and “take your time and don’t rush.”
According to the CCOSH, specialty footwear or training on proper walking and “safe falling” will never be fully effective without adequate housekeeping practices.
Federal regulation
Slip, trip, and fall hazards are addressed in the Occupational Safety and Health Administration’s (OSHA) walking-working surfaces standards (29 Code of Federal Regulations (CFR) Part 1910 Subpart D). In 2016, OSHA issued a final rule revising subpart D to incorporate advances in technology, industry best practices, and national consensus standards to ensure cost-efficient and effective worker protection. The revised rule requires employers to inspect walking-working surfaces regularly to correct, repair, or guard against hazardous conditions.
OSHA defines a “walking-working surface” as “any horizontal or vertical surface on or through which an employee walks, works, or gains access to a work area or workplace location.” Ensure aisles and walkways in your facility are kept clear of slipping or tripping hazards that lead to falls on the same level.
Leave a Reply Cancel reply
Your email address will not be published. Required fields are marked *
Save my name, email, and website in this browser for the next time I comment.
This site uses Akismet to reduce spam. Learn how your comment data is processed .
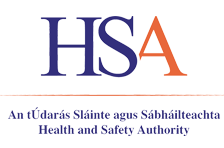
Healthy, safe and productive lives and enterprises
- Accident and Dangerous Occurrence Reporting
- Accreditation
- Introduction
- Justification
- Irish Legislation, EU Directives & Standards
- Delivery Guide
- Design-Construction-Handover
- Functional Safety
- EPD Guidance
- International/European Committees
- National Projects
- Useful Links
- Useful Tools
- ATEX Regulations - Frequently Asked Questions
- What are Biological Agents?
- Classification of Biological Agents
- Biological Agents Frequently Asked Questions
- Good Occupational Hygiene
- Disinfectants
- Vaccination - Frequently Asked Questions
- Transporting Biological Agents
- Biological Agents and Reproductive Health
- Relevant Legislation
- Code of Practice
- Notification
- Accident, Incident and Disease Reporting
- Avian Influenza
- Blood Borne Viruses
- SARS-CoV-2 and COVID-19
- Legionellosis
- Leptospirosis
- Lyme Disease
- Tuberculosis
- Microbiological Safety Cabinets
- Health Surveillance
- Occupational Exposure Lists
- Personal Protective Equipment
- Useful Resources
- Brexit and Access of Products to the EU Market
- Chemicals Export / Import Regulation
- Market Surveillance – Industrial Products
- Selling Goods on the EU Single Market after Brexit
- Transportable Pressure Equipment
- Further information
- Employer Policy
- Are You Being Bullied
- Codes of Practice
- Bullying Employer Perspective
- Bullying Employee Perspective
- Accident/Incident Reporting
- ADR and TPED
- Biological Agents
- Construction
- Other Licensing Agencies
- All Notification Forms
- Classification and Labelling
- Confined Spaces
- Consultation
- Display Screen Equipment
- Managing Safety in Schools
- Teacher Support and Resources
- Teacher Training
- Initiatives in Education
- Electrical Fatality Statistics
- Electricity in the Workplace
- IS 10101 National Rules for Electrical Installation
- Works Needing Certification
- Overhead Power Lines
- Underground Cables
- Video - Dangers from Power Lines on Farms
- Role of the Commission for Regulation of Utilities
- HSA & Other Organisations
- Employees Duties
- Fire Detection and Warning
- Emergency Escape and Fire Fighting
- Fire Prevention
- First Aid Frequently Asked Questions
- Electricity
- Pedestrian safety
- Manual Handling Hazards
Slips, Trips and Falls
- Working at Height
- Lone Workers
- Myth 1: Inspections and Fines
- Myth 2: Health and Safety is Expensive
- Myth 3: Red Tape Hindering Business
- Myth 4: Manual Handling Training
- Myth 5: Everything Banned
- Horticulture
- Human Factors
- Illness Reports
- HSA Inspections
- Recording Inspections
- What to Expect When the Inspector Calls
- Actions of Inspectors
- Powers of Inspectors
- Workplace Fatalities
- The Appeals Process
- Prosecutions 2018
- Prosecutions 2017
- Prosecutions 2016
- Prosecutions 2015
- Prosecutions 2014
- Prosecutions 2013
- Prosecutions 2012
- Prosecutions 2011
- Prosecutions 2010
- Prosecutions 2009
- Prosecutions 2008
- Prosecutions 2007
- On Indictment
- Liquid Petroleum Gas (LPG)
- Safety, Health and Welfare at Work Act 2005
- Safety and Health Management Systems
- Safety Representatives and Consultation
- Safety Statement and Risk Assessment
- Manual Handling Guidance Documents
- Manual Handling Case Study Video Series 1
- Manual Handling Case Study Video Series 2
- Manual Handling FAQ's
- Manual Handling Research reports
- Selling Goods on the EU Single Market
- Joint Market Surveillance Action on HARmonised Products 2021 Omnibus (JAHARP2021 Omnibus)
- Motor Factors
- Respiratory Protective Equipment
- Noise at Work
- Noise - Frequently Asked Questions
- Safe Maintenance - Reducing Noise
- Health Surveillance – Noise
- Vibration at Work
- HAV Risk Assessment
- Optical Radiation at Work
- Electromagnetic Fields
- Agency Roles
- Posted Workers
- Prosecutions
- Public Consultation
- Remote Working
- Safety Alerts
- Frequently Asked Questions
- Safety Signs
- General Simple Safety
- Simple Safety in Retailing
- Simple Safety in Food and Drink
- Simple Safety in other Languages
- STF Online Courses
- Further Information
- Mapping Hazards
- Stairs and Steps
- Slippery Surfaces
- Identify Risks
- Measuring Slip Resistance
- Selecting Surfaces
- Information with Flooring
- Metal and Profiled Surfaces
- Communicate
- Housekeeping
Shoes, Footwear
- Communication
- Sample Risk Assessment
Over-used Signs
- Fatal Injury
- Non-Fatal Injury and Illness
- Agriculture, Forestry and Fishing
- Mining and Quarrying
- Manufacturing
- Electricity; Gas, Steam and Air Conditioning Supply
- Water Supply, Sewerage, Waste Management and Remediation Activities
- Wholesale and Retail Trade; Repair of Motor Vehicles and Personal Goods
- Transportation and Storage
- Accommodation and Food Service Activities
- Information and Communication
- Financial and Insurance Activities
- Real Estate Activities
- Professional, Scientific and Technical Activities
- Administrative and Support Service Activities
- Public Administration and Defence; Compulsory Social Security
- Human Health and Social Work Activities
- Arts, Entertainment and Recreation
- Other Service Activities
- Annual Review of Workplace Injury, Illness and Fatality Statistics
- Other Statistical Reports
- European Statistics on Accidents at Work
- CSO Labour Force Survey Data
- Sun Protection
- Ventilation
- Vulnerable Workers
- Welfare Payments
- Winter Readiness
- Work at Height
- Work Positive Project 2008/2009
- Work Positive Project 2005-2007
- Stress in the Workplace
- Legal Requirements
- Work Related Vehicle Statistics
- Vehicle Risks
- Forklift Trucks
- Transport of Dangerous Goods by Road (ADR)
- Managing Health and Safety
- Liabilities of Directors
- Protecting your Workplace's Reputation and Assets
- Benefits of Creating a Positive Safety Culture
- Organising Safety and Health in your Workplace
- Safety and Health Monitoring
- Roles and Responsibilities for Directors
- Precautions & Risk Assessment
- Legislation & Enforcement
- Agriculture Code of Practice
- Online Risk Assessment FAQs
- Updated Agriculture Safety Videos
- Farm Safety Partnership Advisory Committee
- ATVs / Quad Bikes
- Guidance on the Safe Handling of Cattle on Farms
- Safe Handling of Cattle on Farms Information Sheet
- Cattle Handling in Marts and Lairages
- Children's Book 'Stay Safe on the Farm with Jessy'
- Farm Safety During Lambing
- Sábháilteacht Feirme le linn Breith Uain
- Farm Safety During Calving
- Sábháilteacht Feirme le linn Breith Lao
- Using Petrol Driven Chainsaws
- Chainsaw Felling of Large trees
- Selecting & Monitoring of Contractors
- Mechanical Harvesting
- Extraction by Forwarders
- Electricity at Work
- Chainsaw Snedding
- Cross Cutting & Manual Stacking
- Chainsaw Clearance of Windblow
- Felling & Manual Takedown
- Chainsaw Safety Training Advice
- Forest Owners & Managers who intend to fell trees - Info Sheet
- Code of Practice for Managing Safety & Health in Forestry Operations
- Child Tractor Safety
- Farmers over 65 Years
- Falls & Collapses
- Farmer Health
- Fire Electricity & Chemicals
- Manual Handling Slips & Trips
- Timber Work
- Video Index
- Online Farm Safety Course
- FarmFamilyCPD.ie
- Hospitality General
- Leisure Areas
- Larger Machinery
- Simple Safety
- Role Finder Tool
- Chemicals A-Z
- BeSmart Risk Assessment Tool
- Chemicals Act Guidance
- ECHA Guidance & FAQs
- ECHA Website
- ECHA Webinars
- E-Bulletin Archive
- Helpdesk Information
- Pesticides Control
- Poison Centre
- ADR - Carriage of Dangerous Goods by Road
- What is Asbestos
- Asbestos Surveys
- Latest News
- Safety Alert
- Asbestos FAQs
- Asbestos risks in safes and fire resistant cabinets
- E-Learning Course
- Asbestos Legislation
- Restrictions and Exemptions
- Guidance Document
- Asbestos Removal
- Analysts and Laboratories
- Asbestos Notifications
- Asbestos Waivers
- Other Agencies with Responsibility for Asbestos
- The Chemicals Act
- What are Chemicals Agents?
- Risk Assessment
- What are Carcinogens, Mutagens and Reprotoxic Substances ?
- Roadmap on Carcinogens
- REACH Restriction
- Information for Suppliers and Retailers
- Training Requirements
- Posters (Available in Several Languages)
- Health Surveillance and Monitoring
- Introduction to Welding
- Welding Risk Assessment
- Case Studies
- Chemical Agents Legislation
- Carcinogens, Mutagens and Reprotoxic Substances Legislation
- Chemical Weapons
- Classification
- Introductory Guidance on the CLP Regulation
- CLP Regulation (EC) No 1272/2008
- Understanding CLP
- Publications and Guidelines
- External Resources
- Health Hazards
- Environmental Hazards
- Notification to NPIC
- Notification to the C&L Inventory
- Roles and Duties
- Introduction to COMAH
- Legislation
- Inspections
- Useful Links on Major Accidents
- Notifications
- MAPP and Safety Management
- Safety Report
- Timelines for Submission of COMAH Documentation
- Significant Modifications
- Reporting COMAH Accidents
- Information to the Public Overview
- List of all Establishments by Tier
- Lower Tier Establishments by County
- Upper Tier Establishments by County
- Objectives of Emergency Plans
- Testing and Review of Emergency Plans
- Local Competent Authority Annual Report
- Internal Emergency Planning
- External Emergency Planning
- Role of the HSA in Land-use Planning
- Consultation Distance
- Societal Risk
- Request for Technical Advice
- HSA Approach to Land Use Planning
- COMAH Regulations 2015
- Guidance on Technical Land-use Planning Advice
- MAPP Guidance for Lower Tier Operators
- Intermediate Temporary Storage
- LCA Annual Report on Activities
- Electronic Notification
- Request for TLUP Advice
- Schedule 7 Notifiable Incident
- LCA Annual Report of Activities
- MAPP Assessment form for Lower Tier Establishments
- News Updates
- What are Detergents
- Detergent Regulations
- Detergent Labelling & Packaging requirements
- Using and Storing Detergents
- Ingredient Data Sheets
- Liquid Laundry Detergent Capsules
- Biocidal detergent products
- EU Derogation for Surfactants
- EU Chemicals Strategy for Sustainability Conference 2023
- DNAs in Ireland
- Obligations of EU Exporters
- Obligations of EU Importers
- Chemicals Subject to Export/Import Notification
- The Role of the Authority
- Nanomaterials
- Roles and duties under REACH
- SVHCs and Authorisation
- How does a chemical get onto Annex XVII of REACH
- Annex XVII Updates of REACH
- Information in the Supply Chain
- Notification of Substances in Articles
- The registration process
- Only representative
- Duty to inquire
- Downstream users
- Questions and Answers
- EU enforcement projects to check poison centre notifications & online sales
- New CLP hazard classes will be included in IUCLID
- Have Your Say - ECHA seeks comments on proposals to identify 2 more chemicals as substances of very high concern under REACH
- ECHA provides advice on new hazard classes for substances and mixtures
- PFAS restriction proposal
- New obligations for sale of Diisocyanate products from 24th August 2023
- EU-wide project found excessive levels of hazardous chemical in products sold to consumers
- ECHA have published the Draft CoRAP for 2024-2026- for 2024 proposed substances’, registrants are encouraged to update their dossiers before March 2024
- HSA information sheet on regulatory obligations of EU candle and reed diffuser producers
- ECHA adds five hazardous chemicals to the Candidate List
- ECHA consults on recommending five substances for REACH authorisation
- Selling chemical products online
- Poison Centre Notification
- Obligations for producers of candles/diffusers
- Safety Data Sheets
- Keep your registration up to date
- Chemical Risk Assessment
- Read the back
- REACH Authorisation List
- REACH Candidate List
- Paint containing MEKO
- Candles and reed diffusers containing LILIAL
- ECHA & EU Consultations
- HSA Consultations
- Project Supervisor Design Process (PSDP)
- Project Supervisor Construction Stage (PSCS)
- Contractors
- Create a Site Specific Safety Statement
- Create a Construction Stage Safety and Health Plan
- Risk Assessment Method Statement (RAMS) Template and Guidance
- Create a Construction Site Traffic Management Plan
- Information for Employees
- Other Useful Resources
- hsalearning.ie for Construction
- Construction Skills Certification Scheme (CSCS)
- Duties as a Designer
- Good Design Practice
- Construction Site Traffic Management Plan
- Safe use of Dumpers
- The Lighthouse Club
- Construction Workers Health Trust
- CAIRDE On Site. In Mind.
- Construction Safety Partnership Advisory Committee
- Construction Regulations Amendment 2019
- Auxiliary Devices
- Safety File
- Excavations
- Diving at Work
- Hiring Diving Contractors
- Diving Methods
- Dive Team Size
- Diving Training
- Compression Chambers
- Emergency Equipment
- Diving Medicals
- Fitness to Dive
- Mutual Recognition
- Diving and Pregnancy
- Reporting Accidents and Dangerous Occurrences
- Underwater Heritage Orders
- Health and Safety Management
- Emergency Plans
- Docks Code of Practice
- Common Hazards
- Container Terminals
- Dry Bulk Terminals
- Roll On Roll Off (Ro-Ro) Terminals
- Useful Websites & Publications
- Legislation and Enforcement
- Who's Who in Fishing Safety
- Maritime Legislation
- The Sea Fishing Sector
- Top 10 Tips
- Management of Health and Safety
- Emergency Contacts
- The Safety Statement
- Safe Systems of Work
- Instruction, Training and Supervision
- Injuries and Ill Health
- Slips and Trips
- Manual Handling
- Dangerous Chemicals
- Instability
- Publications and Useful Websites
- Lifejackets
- Regulations
- Information and Guidance
- The Health and Social Care Sector
- Health and Social Care Regulators
- Health and Social Care Illness and Injury Statistics
- Sharps Directive and Regulations
- Healthcare Waste
- Specific Biological Agents
- Chemical Agents
- Electricity and Healthcare
- Musculoskeletal Disorders
- Slips Trips and Falls in Healthcare
- Work Related Stress
- Violence and Aggression
- Work Equipment
- Emergency Department
- Ambulance Services
- Outpatients
- Stores / Warehouse
- Technical Services
- Maintenance Workshop
- Lounge / Activity Room
- Sluice Room
- Garden / Grounds
- Nurse's Station
- Hallway / Corridor
- Mining Legislation and Notifications
- Promotional Activities
- Disused Mines and Shafts
- Mines Rescue
- Mining in Ireland
- Mining Techniques Used in Ireland
- Managing for Health and Safety
- Health and Safety in Education Sector
- Heath and Safety in Healthcare Sector
- Health and Safety in Central Government
- Health and Safety in Local Government
- HSALearning
- Healthy Ireland
- State Claims Agency
- Chemical Exposure
- Dust Including Silica Dust
- Noise in Quarries
- Whole Body Vibration
- Muscoskeletal injury
- Quarry Accident and Inspection Statistics
- What to Expect from an Inspection
- HSA Quarry Sector Resources
- Safe Quarry Guidance
- Statutory Notifications
- Quarries Legislation and Guidance
- Quarry Workers Guide
- Other Quarry Industry Groups
- Publications and Videos
- Quarry Safety Week
- All Island Seminar 2018 Exhibitors Info
- All Island Seminar 2018 Delegates
- Vehicle Access
- Driver Selection and Training
- Construction of Haul Roads
- Reversing and One-way Systems
- Selection of Equipment
- Inspection of the Working Face
- Significant Hazards
- Overburden Stripping
- Trespass, Boundary Fencing and Prevention of Drowning
- Drilling of Shotholes
- Danger Zones
- Disposal of Surplus Explosives
- Blast Specification
- Duties of Shotfirer
- Face Profiling and Drill Hole Logging
- Edge Protection during drilling and loading
- Management of Lagoons and settling ponds
- Management of Tips and Stockpiles
- Inspection, Appraisal and Geotechnical assessment
- Asphalt Plant Safety
- Machinery and Conveyor Initiative 2020
- Work Permits and Isolation of Equipment
- Tyre Changing and Repair
- Workshop Safety
- Maintenance Work at Height
- Guarding Return Idler Rollers
- Mobile Crushing and Sizing
- Conveyor Guarding and stops - pull wires
- Clearing Blocked Crushers
- Batching Concrete, Block and Asphalt Plants
- Renewable Energy
- Taking Care of Business
- Getting Started
- Safety Statement
- Recommended Publications
- Micro Business
- Vehicle Incident Trends
- Work Related Vehicle Safety
- Workplace Transport Safety
- Working on or near a road
- Driving for work
- Vehicle Maintenance
- Chemical Agents and Carcinogens
- Information to the Public
- Export / Import
- Nanotechnology
- Chemicals Acts 2008 and 2010
- Chemical Weapons Act 1997
- Organisation of Working Time Act 1997
- Safety Health and Welfare (Offshore Installations) Act 1987
- Safety in Industry Act 1980
- Dangerous Substances Act 1972
- European Communities Act 1972
- Factories Act 1955
- Code of Practice for the Chemical Agents Regulations
- Code of Practice for Preventing Injury and Ill health in Agriculture
- Farm Safety Code of Practice - Risk Assessment document
- Code of Practice for the Design and Installation of Anchors
- Code of Practice for Working in Confined Spaces
- Working on Roads Code of Practice - for contractors with three or less employees
- Code of Practice for Avoiding Danger from Underground Services
- Code of Practice for Safety in Roofwork
- Code Of Practice for Biological Agents
- More Codes of Practice
- Online Complaint Form
- Agriculture
- Chemical and Hazardous Substances
- Docks and Ports
- General Application Regulations
- Health and Social Care Sector
- Information Sheets
- Latest Publications
- Machinery and Work Equipment
- Manual Handling and Musculoskeletal Disorders
- Mines and Quarries
- Occupational Health
- Physical Agents
- Research Publications
- Safe System of Work Plan (SSWP)
- Safety and Health Management
- Slips Trips and Falls
- Work Related Vehicles
- EU Weekly RAPEX Alerts
- The Benefits
- Risk Assessments Made Easy
- Safety Statements Made Simple
- hsalearning.ie
- Work Positive
- Publications, Top Tips and Videos
- Workplace Health Toolkit for Businesses
- Simple Safety Series
- Safety Representatives
- New Publications and Resources
- Resources in Different Languages
- Post-Primary Guidelines
- Post-Primary Guidelines - Safety Statement Checklist Word Documents
- Post-Primary Guidelines - Safety Statement Checklist PDFs
- Post-Primary Guidelines - Part B - FAQs
- Post-Primary Guidelines - Part C - Risk Assessment Templates
- Primary Schools Guidelines - Short Guide
- Primary Schools Guidelines
- Video on Primary School Guidelines
- Interactive Risk Assessments – Primary
- Treoirlínte ar Bhainistiú Sábháilteachta, Sláinte agus Leasa i mBunscoileanna
- Treoirlínte maidir le Bainistiú Sábháilteachta, Sláinte agus Leasa in Iar-Bhunscoileanna
- 'What's Under the Sink?' Household Chemicals SPHE Presentation – Primary students
- 'What's Under the Sink?' – Primary teacher guidelines
- Farm Safety Presentation - Primary teachers
- On the Farm Videos - Primary students
- Choose Safety / Get Safe Work Safe - Transition Year teachers / students
- Choose Safety – Post Primary / Further Education
- Keep Safe on the Farm – Post Primary students
- Graduate.ie – Post Primary students
- Roghnaigh an tSábháilteacht
- Post Primary
- Choose Safety
- Courses for Apprentices on hsalearning
- Workplace Health and Safety Induction hsalearning course
- Get Safe Work Safe hsalearning course
- Mainstreaming
- Only a Giant can Lift a Bull
- Too Cold for Sharks
- Health and Safety Training Providers
- Online Course for Schools
- Online Courses for Students
- Your Safety, Health and Welfare in Healthcare - Online Course
- Online Course Information Leaflets
- Safety, Health and Welfare Induction
- New Resources
- Translated Resources
- Work Related Vehicles Safety Program Plan and Priorities for 2016-2018
- Public Consultation on new Code of Practice - Safe Industrial Truck Operation
- Vehicle Related Accident Trends
- Falls from Vehicles
- Vehicle Overturns
- How to Manage Work Related Road Risks
- Online Vehicle Risk Management Resource (EU Commission)
- Winter Driving Tips
- Grey Fleet Driver Declaration Form
- Managing Grey Fleet Information Sheet
- HSA and UCD joint webinar on Work Related Road Fatalities
- Employer Responsibilities
- Online Course
- Driver Health
- Driver Handbook
- Road Safety Law
- Managing Your Employees
- How to Manage Driving for Work
- Evaluating Road Safety Risks Movie
- Benefits for the Community
- Vehicle Safety Pre-Checks
- Vehicle Risk Management Business Case Studies
- New Guidance – Safe and Efficient Goods Reception for Road Freight
- Managing Workplace Priority Risks
- Workplace Transport E-Learning Courses
- Managing Pedestrians at Work
- Warehousing Safety
- Guidance and Publications
- Load Securing Videos
- Working on Roads Guidelines
- Safety in Road Work Zones - PRAISE Report 2011
- Guidance and Information
- Transport & Storage Sector Incident Trends
- Behaviour Based Safety Guide Part 1
- Behaviour Based Safety Guide Part 2
- Top Ten Tips for Behavioual Safety - Factsheet
- Are you being Bullied ?
- Bullying - Employer Perspective
- Bullying - Employee Perspective
- Ergonomic Risk Assessment Tools
- Manual Handling Videos Series 1
- Manual Handling Videos Series 2
- BeSMART Videos
- Miscellaneous Videos
- Infographics
- Display Screen Equipment FAQs
- Manual Handling FAQs
- Manual Handling Training System FAQs
- Other Links
- Further Reading and Information
- Occupational Dermatitis Frequently Asked Questions
- Occupational Asthma Frequently Asked Questions
- Pregnant at Work Frequently Asked Questions
- Workplace Stress (AKA Work-Related Stress)
- The Role of the HSA
- What is WorkPositiveCI
- What Workplace Stressors does WorkPositiveCI Measure
- How to Implement WorkPositiveCI in your Workplace
- Guidance - Work-related Stress a Guide for Employers
- Guidance - Work-related Stress Information Sheet for Employees
- Managing Psychosocial Hazards in the Workplace Information Sheet
- Healthcare - Work-related Stress Webpage
- Homeworking - Managing Stress whilst Working from Home
- Podcast - Questions and Answers on Stress and Bullying at Work
- HSE (UK) Management Standards on Work-related Stress
- Job Stress and Working Conditions Report (2019) ERSI
- Healthcare - Work Related Stress Mental Health Promotion in the Healthcare Sector (EU OHSA)
- Practical Advice for Workers on Tackling Work-Related Stress and its Causes (EU OSHA)
- Critical Incident Stress Management Network Ireland
- Higher Executive Officer – Data Analyst
- Board Vacancies
- General Information for Applicants
- Working with the HSA
- Recruitment Policy
- About the HSA
- Social Media
- Webinar Recordings
- Previous Events
- Workers' Memorial Day
- Press Releases 2024
- Contacting the HSA during the COVID-19 crisis
- Media Queries
- Newsletters & Bulletins
- Focal Point Network
- European Healthy Workplaces Campaign 2023-2025
- European Healthy Workplaces Campaign 2020-2022
- European Healthy Workplaces Campaign 2018-2019
- European Healthy Workplaces Campaign 2016-2017
- European Union Senior Labour Inspectors Committee (SLIC)
- HSA on Facebook
- HSA on YouTube
- HSA on LinkedIn
- HSA on Twitter
- Press Releases 2023
- Press Releases 2022
- Press Releases 2021
- Press Releases 2020
- Press Releases 2019
- Press Releases 2018
- Press Releases 2017
- Press Releases 2016
- Press Releases 2015
- Press Releases 2014
- Press Releases 2013
- Media Campaigns
- Board Member Profiles
- Organisational Structure
- Vision, Mission and Mandate
- Strategic Priorities
- Prompt Payment Details
- Purchase Orders in Excess of €20,000
- Financial Statements and Reports
- Why Contact the HSA Contact Centre
- HSA Contact Centre Service Levels
- Make a Complaint
- Protected Disclosures Annual Report
- HSA Contact Centre
- Protected Disclosures
Please Note
Our website uses cookies to enhance your browsing experience and to collect information about how you use this site to improve our service to you. By not accepting cookies some elements of the site, such as video, will not work. Please visit our Cookie Policy page for more information on how we use cookies.
- News, Events & Media
- Customer Service
- RSS News Feed
- Follow HSA on Twitter
- Subscribe to our newsletter
- Bullying at Work
- Business Licensing and Notification Requirements
- Health and Safety Myths
- Market Surveillance
- Personal Protective Equipment - PPE
- Slips Trips Falls
- Workplace Stress
- Work Safely
- Agriculture & Forestry
- Catering and Hospitality
- Flammable liquids and Fuels Retail Stores - NEW
- Public Sector
- Small Business
- Publications
- Employer and Employee Supports
- New Publications and Translated Resources
- Managing Safety and Health in Schools
- Teacher Support And Classroom / Student Resources
- Safety and Health Initiatives in Education
- Health and Safety Courses Online
- Driving for Work
- Load Securing
- Working On or Near a Road
- Transport and Storage
- Accidents and Behaviour
- Manual Handling & Display Screen Equipment
- Occupational Asthma and Dermatitis
- Sensitive Risk Groups
As it gets colder, consider the risk of slipping on ice – see www.hsa.ie/ice
Every working day seven people are hurt in work slips, trips and falls (STF)
- See a systematic approach to Slip Risk Assessment and Prevention
- See our online training on Slips, Trips and Falls and Safer Stairs and Steps
- See our Information Sheets on Preventing Work STF , Safer Work Stairs and Steps , Preventing Vehicles STF and Choosing Slip-resistant Footwear
- See our internet sections on STF Info , High-risk Areas , Spills , Pedestrian Surfaces , Environmental Cleanliness , Footwear , Ice and Over-used Signs
Submission completed, thank you!
Slips trips falls info, high-risk areas.
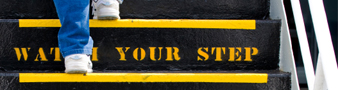
Pedestrian Surfaces
Environmental cleanliness.
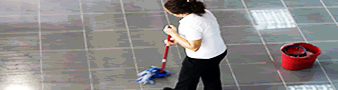
- Floor Wet Cleaning
Snow and Ice
Subscribe to hsa publications, subscribe to hsa chemicals publications.

The Science Behind Slip, Trip, and Fall Prevention
Slip, trip, and fall claims carry a high frequency, but typically, low severity, with their associated costs totaling over $11 billion annually. studies focused on surface interactions, in conjunction with human behaviors, may help determine best practices for preventing these incidents..
September 11, 2023
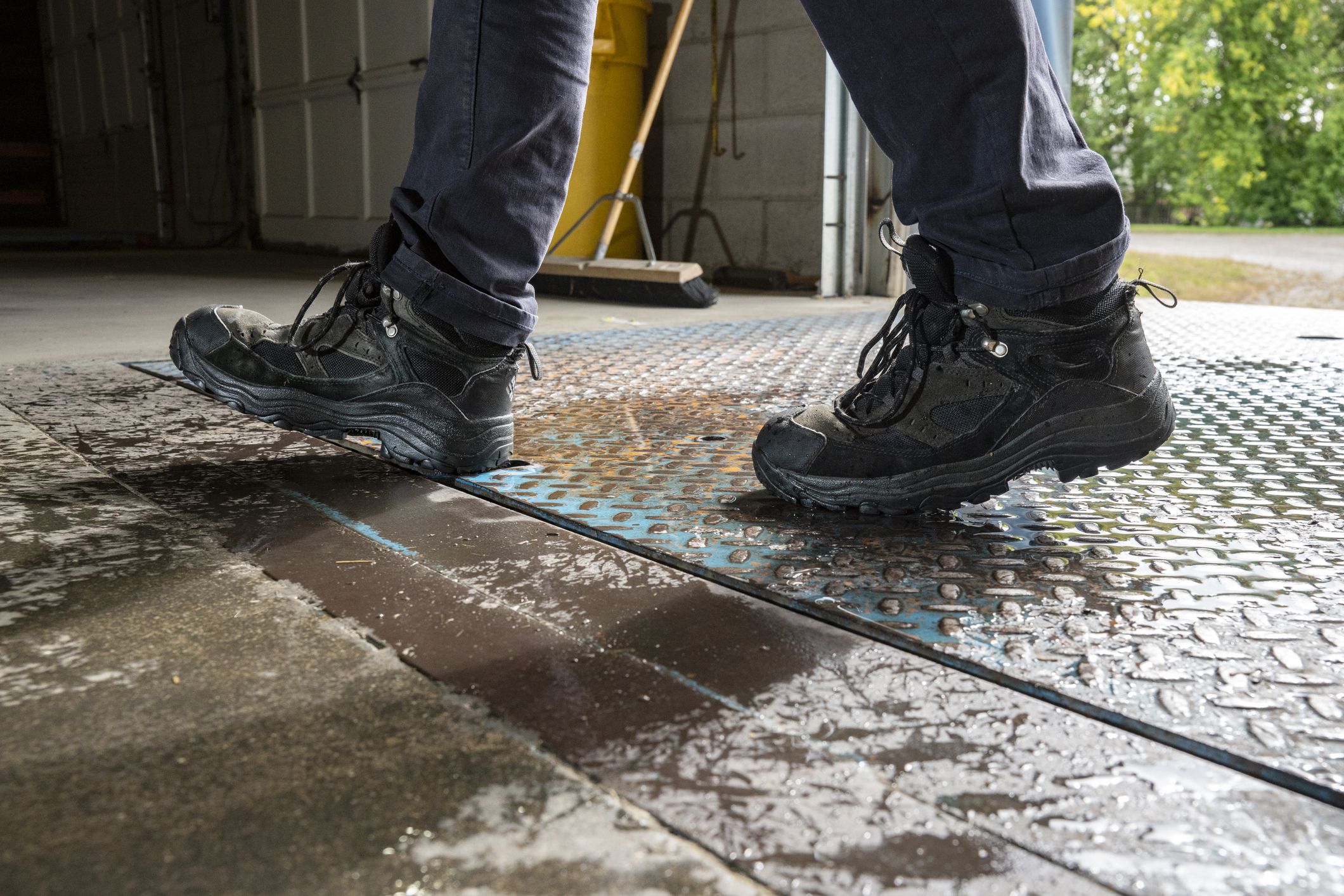
Slipping occurs due to a lack of traction between a foot or shoe sole and the walking surface, but conditions like spills, wet or icy weather elements, or loose rugs or mats are typically common causes of the slip. The science of interacting surfaces in relative motion, known as tribology, can help risk managers understand the importance of proper footwear and floor maintenance, however, there is so much more to account for when understanding why slip, trip, and fall (STF) incidents occur.
“Tribology can get as granular as the direction of the tread to increase traction,” said Sonya Luisoni, Senior Risk Control Manager at Safety National. “Yet, these studies are typically conducted in a lab under a controlled environment, which does not translate into the real world very easily. To understand the full scale of the risk, organizations need a more holistic view that accounts for specifics like age, gender, body mechanics, and health risks.”
Here we examine the types of incidents that happen, and what may cause them outside of tribology practices.
Types of STFs
When examining slips, trips, and falls on the same level (STFL) versus those that occur from heights or stairs, there are several classifications. While the nature of work can vary the types of accidents, these are the most common.
Microslip is a slip shorter than 3 cm and generally goes unnoticed.
Slip is as long as 8-10 cm, resulting in instinctive efforts to regain postural control.
Slide is uncontrolled movement of the heel typically when slip is greater than 10 cm. Likely to lead to a loss of balance and result in a fall.
Trip occurs when the swing phase of the foot is interrupted unexpectedly due to inadequately clearing the ground. Irregularities of as little as 5 mm of walking surface can be sufficient to cause a trip.
Loss of balance can be the result of an unexpected forcible connection with an object or person. It can also occur with forcible movement of the floor itself, as when standing in a moving vehicle.
Stumbling is a consequence of slip, trip or loss of balance and refers to the process of falling and subsequent attempts to regain balance rather than being a triggering event.
Biomechanics Increasing STF Risks
Lab environments are helpful for understanding how footwear tread, floor materials, and weather elements impact traction, but they cannot replicate the myriad of gaits and tasks of an individual. These characteristics that affect the motion of our body, or biomechanics, can severely influence falls and severity.
- Gait: Walking involves a complicated combination of challenging central nervous system (CNS) functions. It is estimated that while walking, 80% of the gait cycle is in a continuous state of instability. The dynamic stability is lost and regained in every gait cycle during normal walking. Recovery from a slip, slide or trip relies on a complex interplay of neural and motor control. There is also a level of expectancy that this natural interplay will keep us safely walking. When the expectation does not meet reality, we interrupt the flow and can end up injured from a slip, slide, or fall injury. That may explain why STFs are more prevalent in older and heavier individuals.
- Work Pace: Increased walking speed reduces dynamic walking stability in part because the faster pace increases the required coefficient of friction (RCOF). If the shoe and floor cannot provide the appropriate friction, there’s a risk of slip, slide or fall. Tripping differs from slipping and sliding in that an object abruptly disturbs the dynamic stability of walking. Recovery from a trip depends on factors such as lower extremity muscular power, ability to restore control of the flexing truck, reaction time, step length and walking speed.
- Load Carrying: Carrying a load can be a major factor contributing to STF injuries. As one would expect, the normal recovery mechanisms we employ to recover from a disturbance have to contend with the additional weight of the load. Often, this correction cannot be accomplished in the split second available before losing control.
For more expertise, guidance or resources on this topic, please contact [email protected] .

RELATED ARTICLES
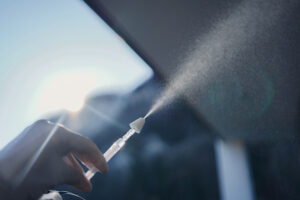
Is Naloxone Guidance the New AED Training?
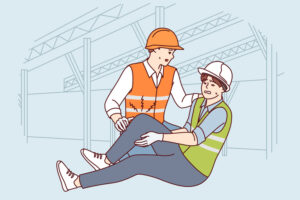
The Link Between On-the-Job Tenure and Injury Rates
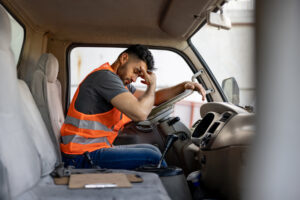
The Dangers of Drowsy Driving
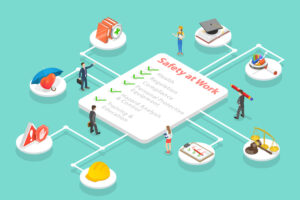
7 Indicators of a Best-in-Class Safety Culture
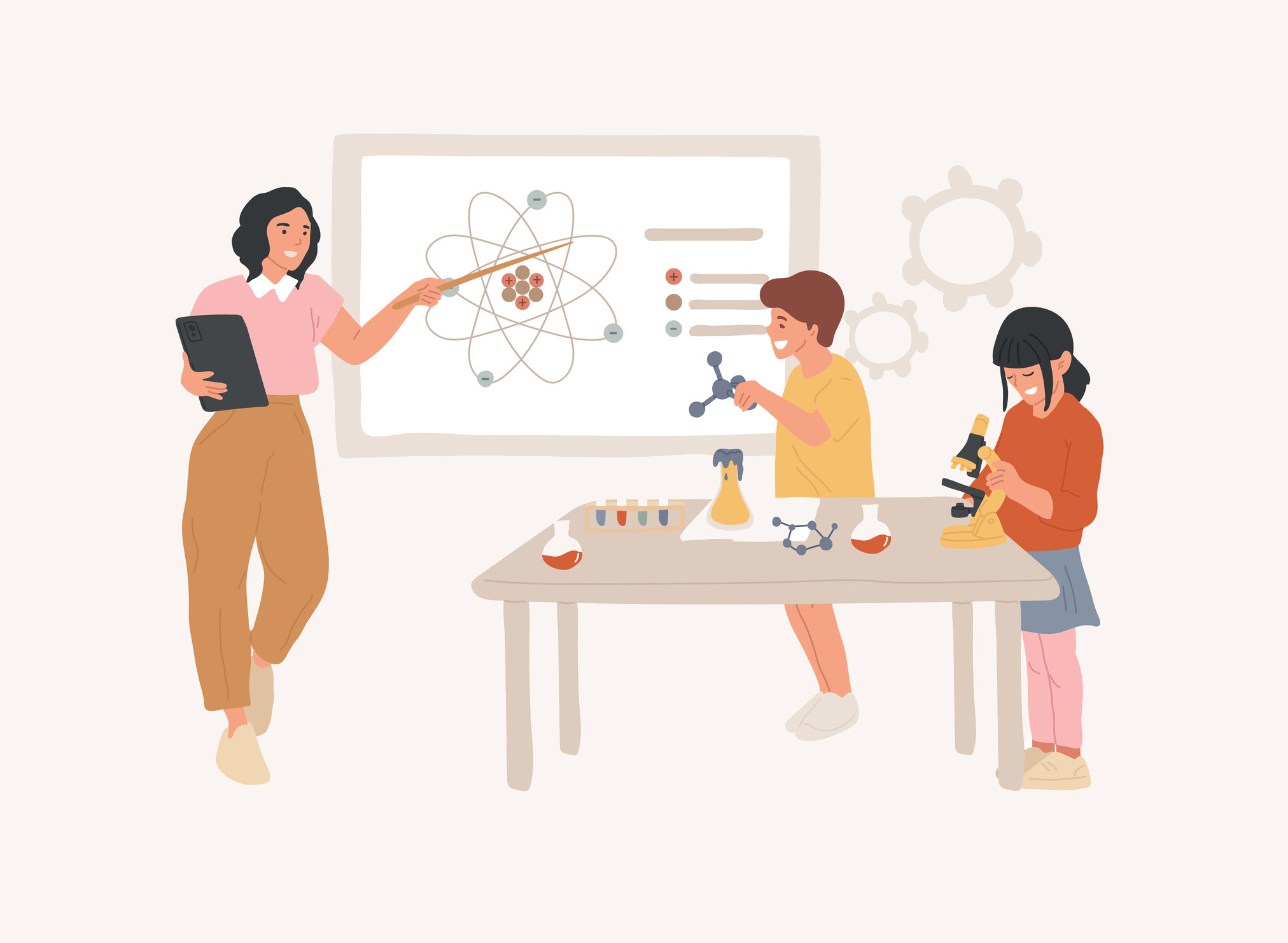
Insights from Losses: Preventing K-12 School Lab Incidents
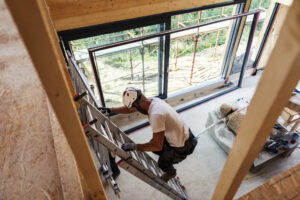
5 Ladder Safety Tips to Take a Step in the Right Direction
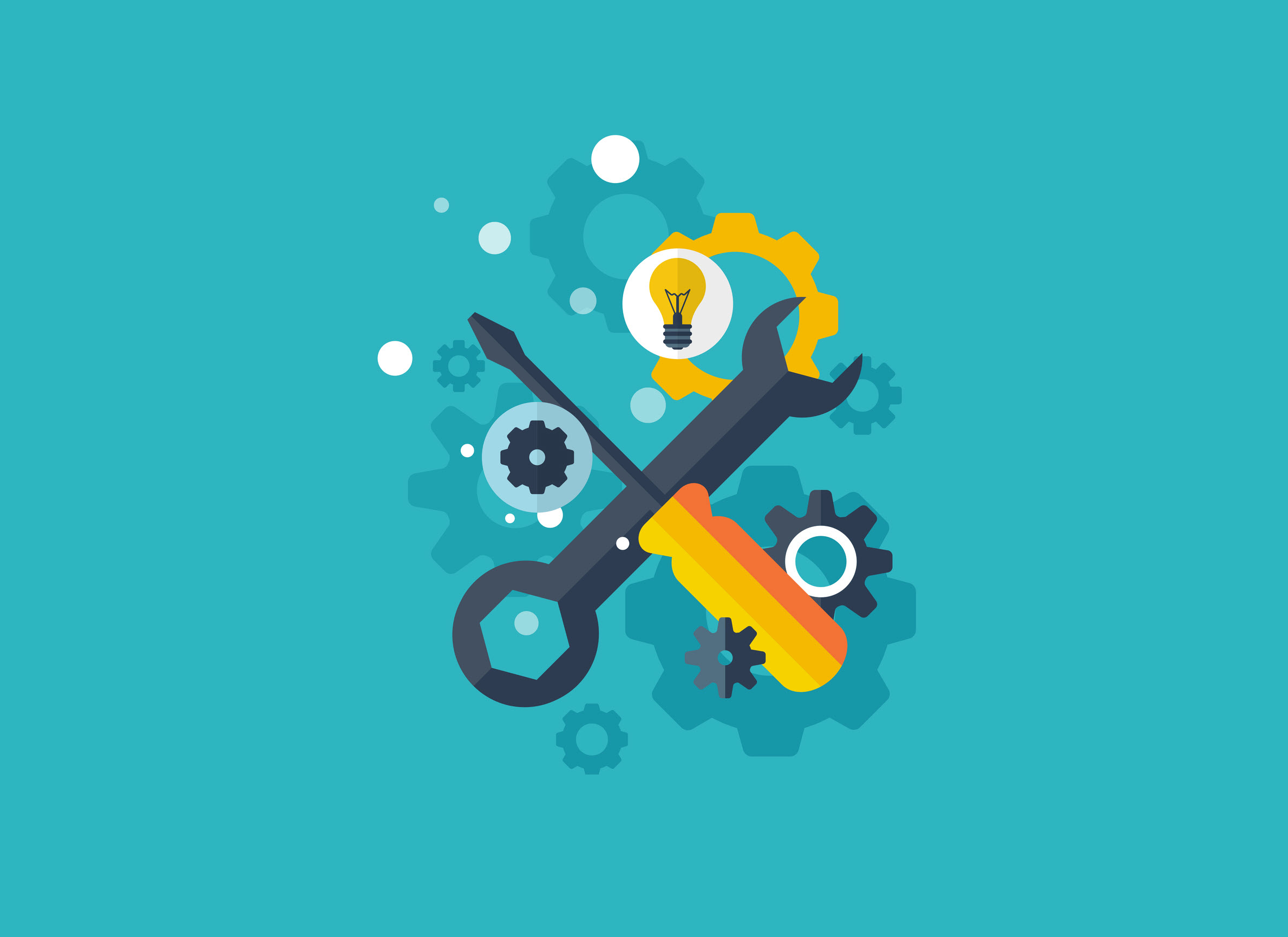
The Top 6 Fleet Safety Program Improvement Strategies (Infographic)
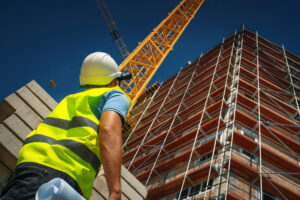
Tactics to Prevent OSHA’s Most Frequently Cited Safety Standards
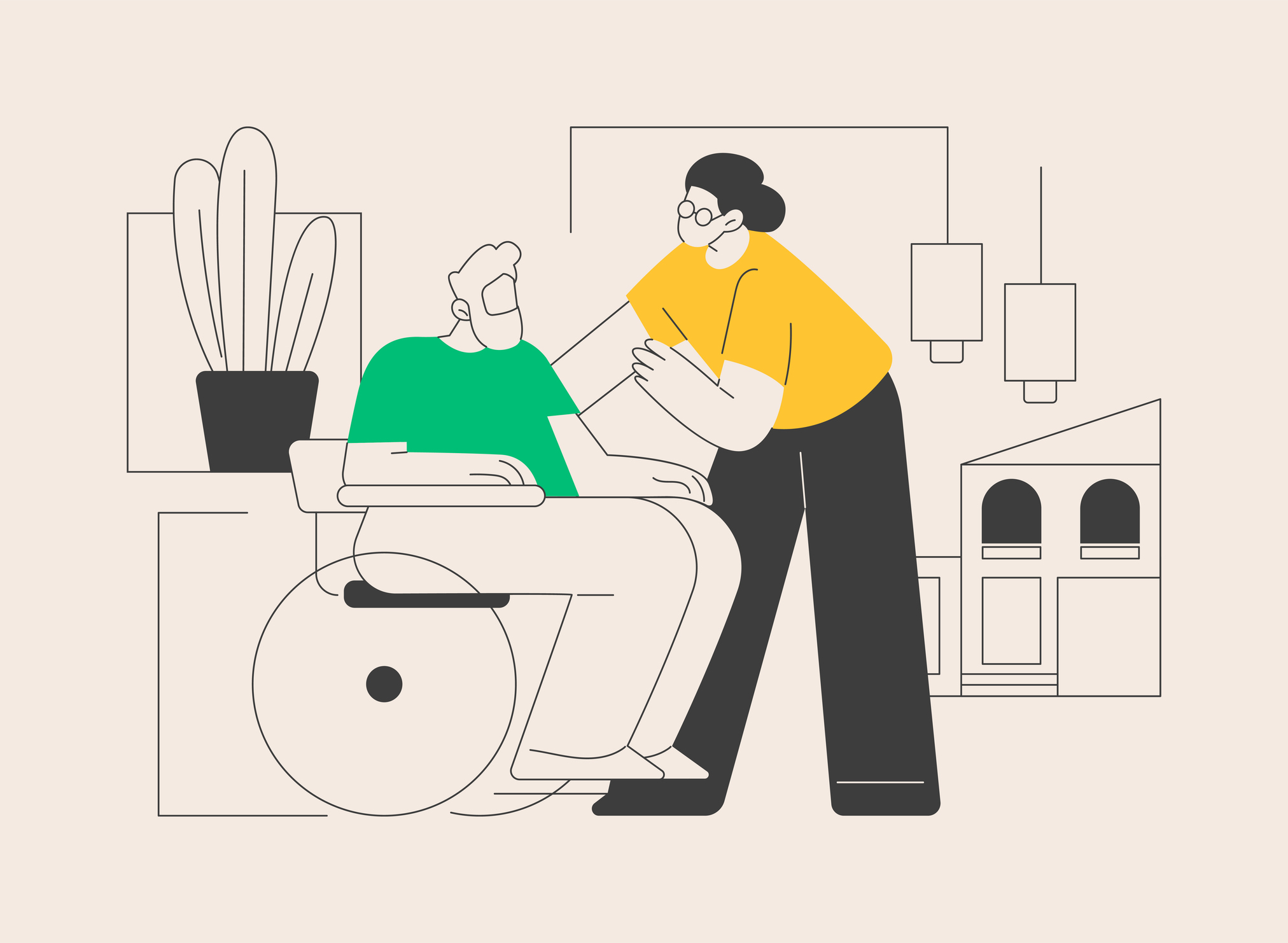
3 Reasons for Healthcare Facilities to Prioritize Safe Patient Handling
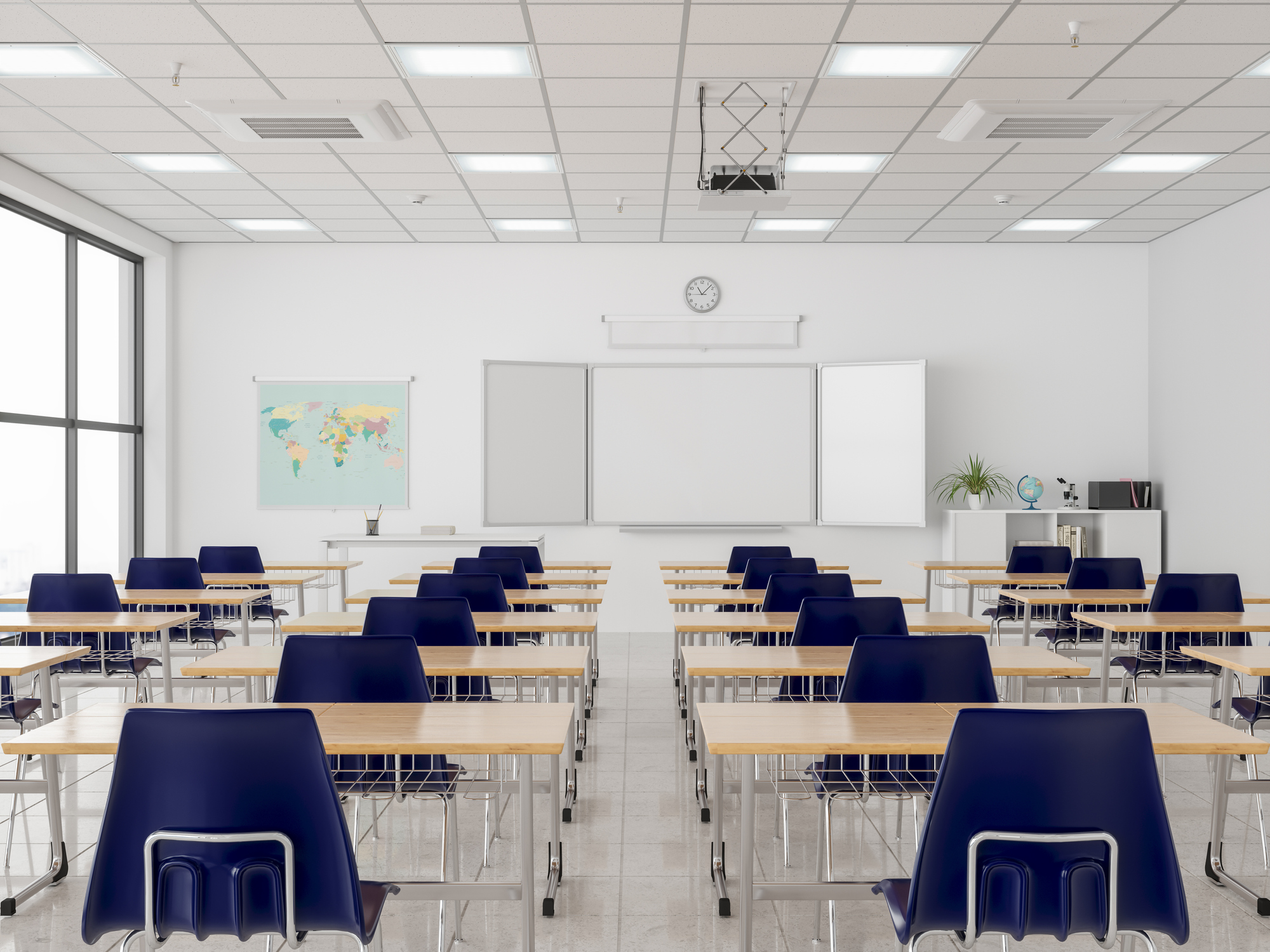
How to Apply Enterprise Risk Management in K-12 Education
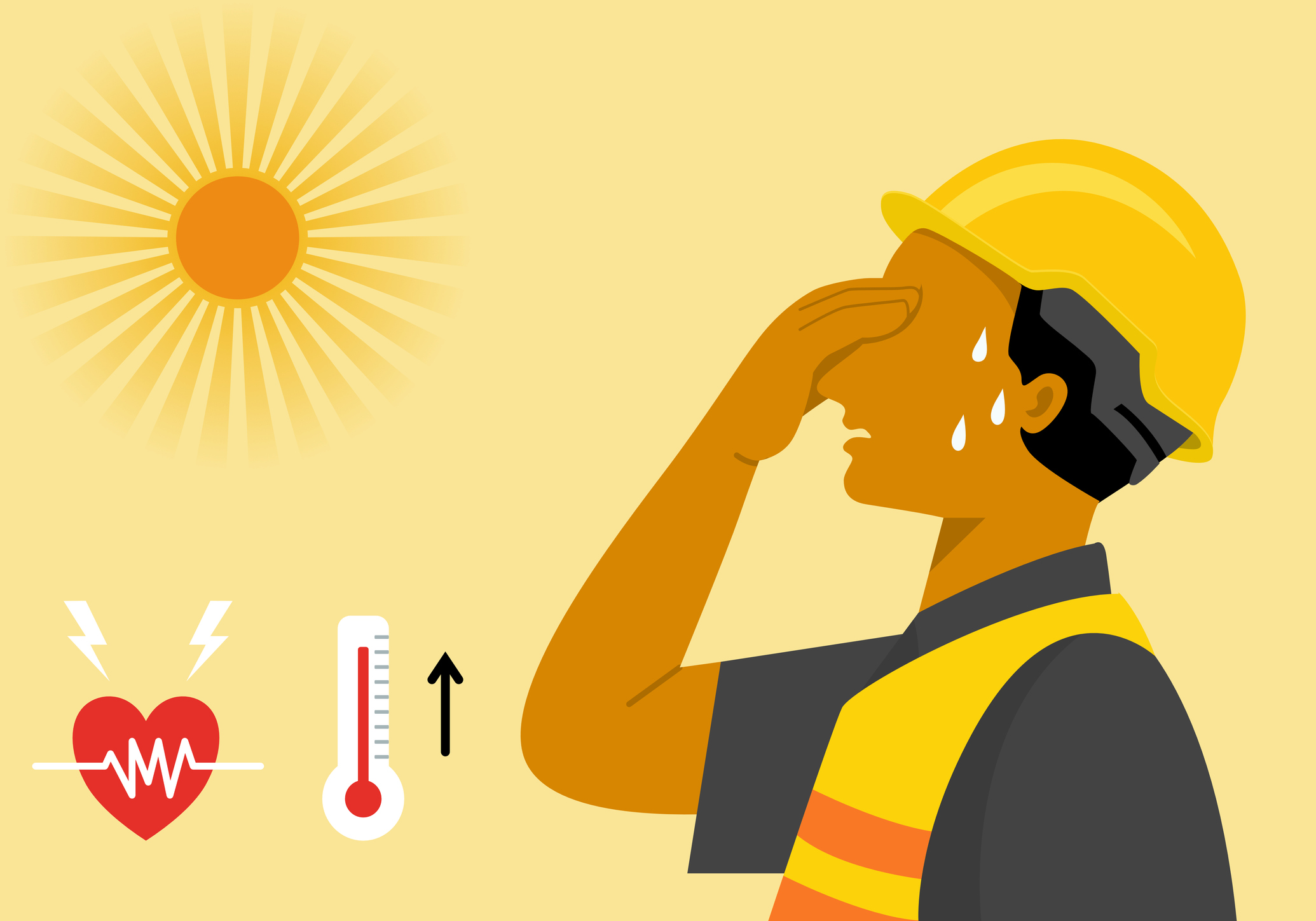
6 Advanced Capabilities of Wearable Technology
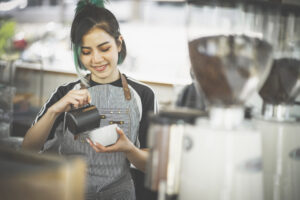
Are You Protecting Your Young Workers?
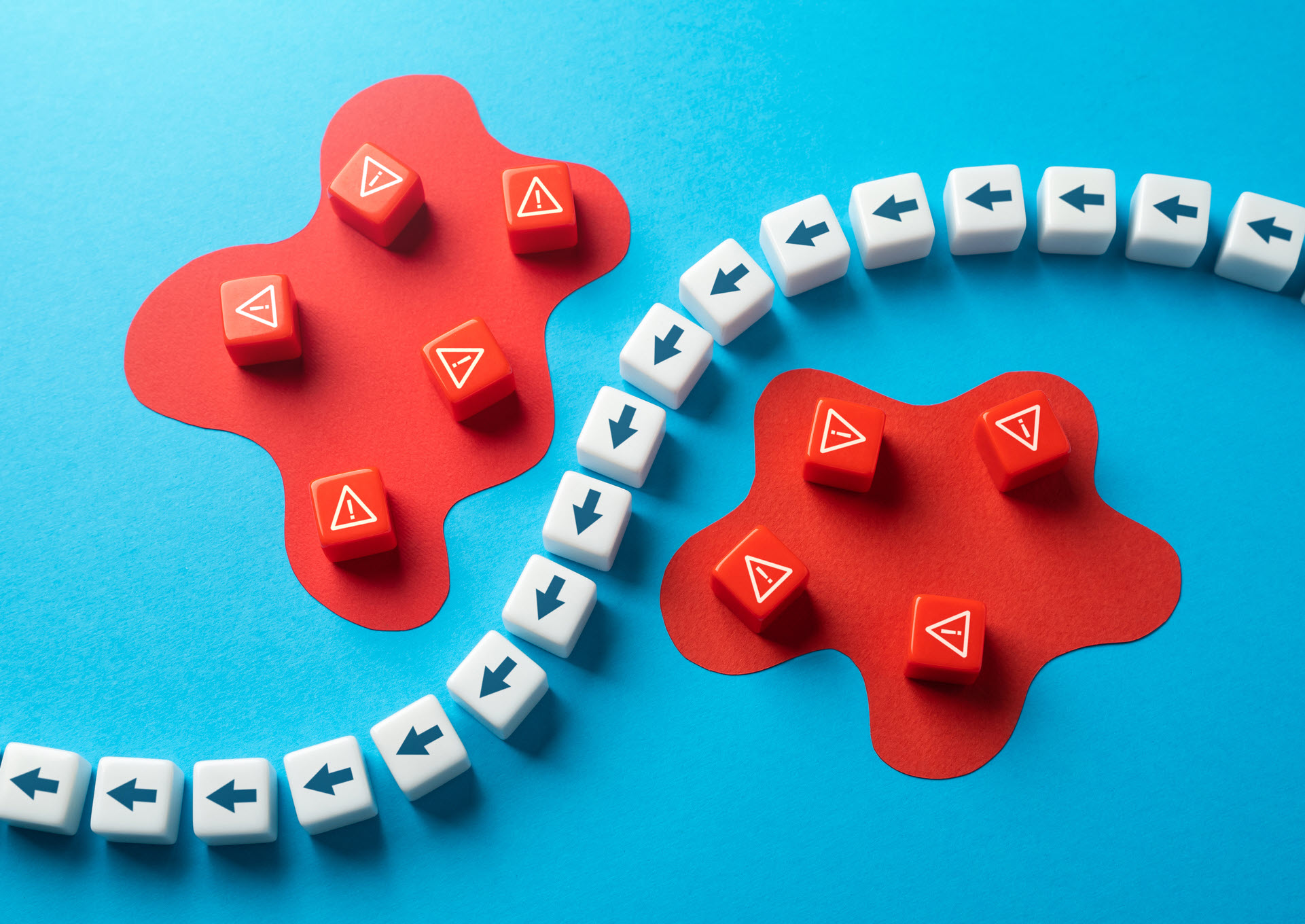
Why Your Organization Needs a Near-Miss Management System
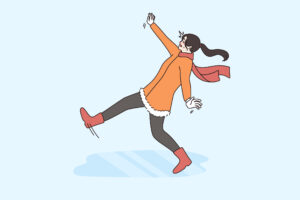
Address This Major Risk to Help Prevent Costly Premises Liability Claims
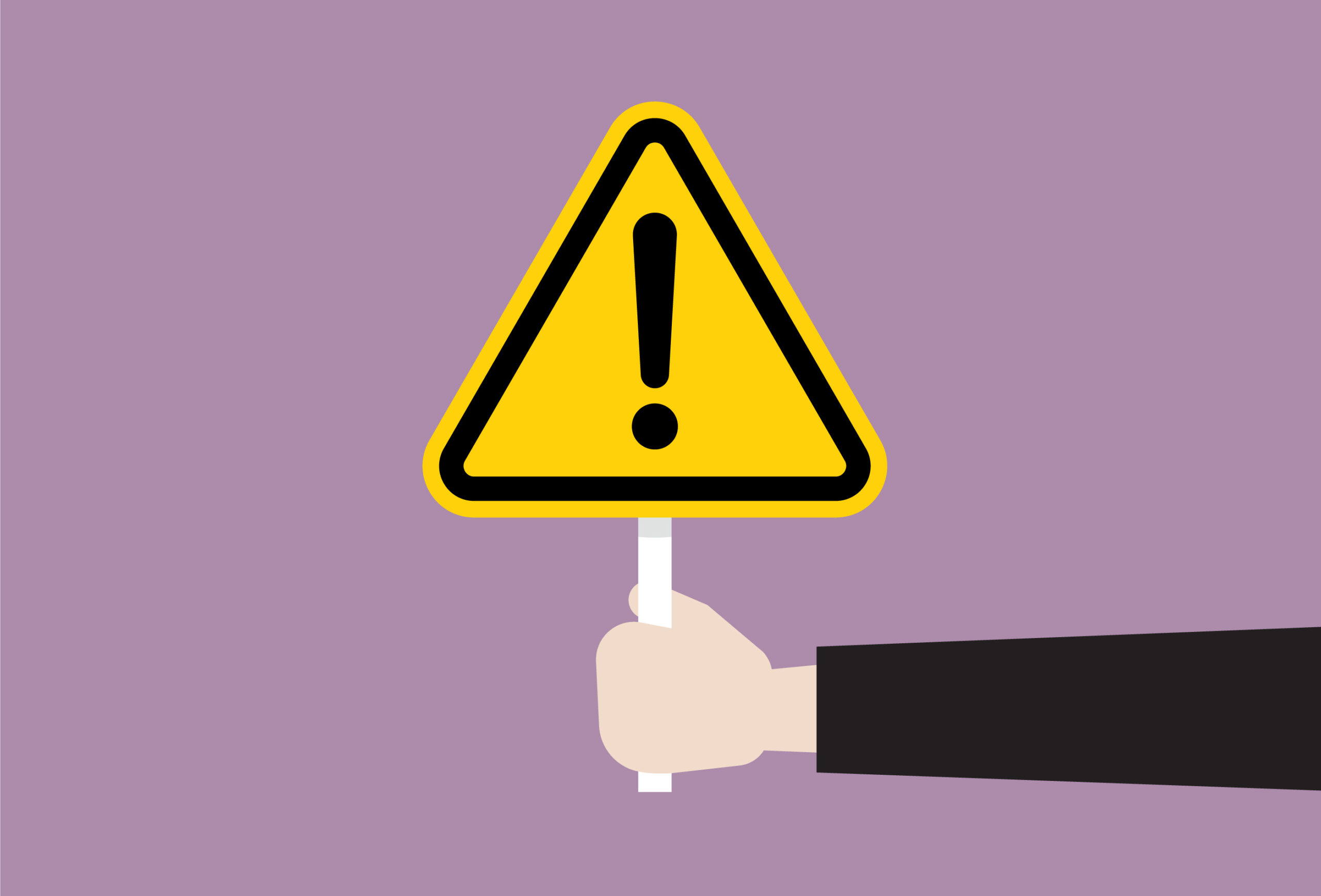
How to Improve Situational Awareness in Your Workforce
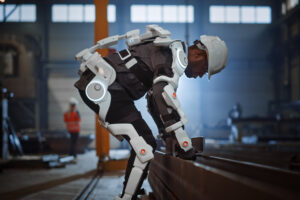
Your Wearable Tech Questions Answered
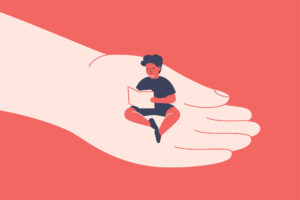
5 Steps to Safeguard Students by Preventing Sexual Abuse
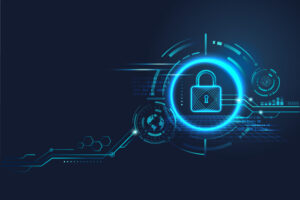
What a Great Cyber Policy Should Cover
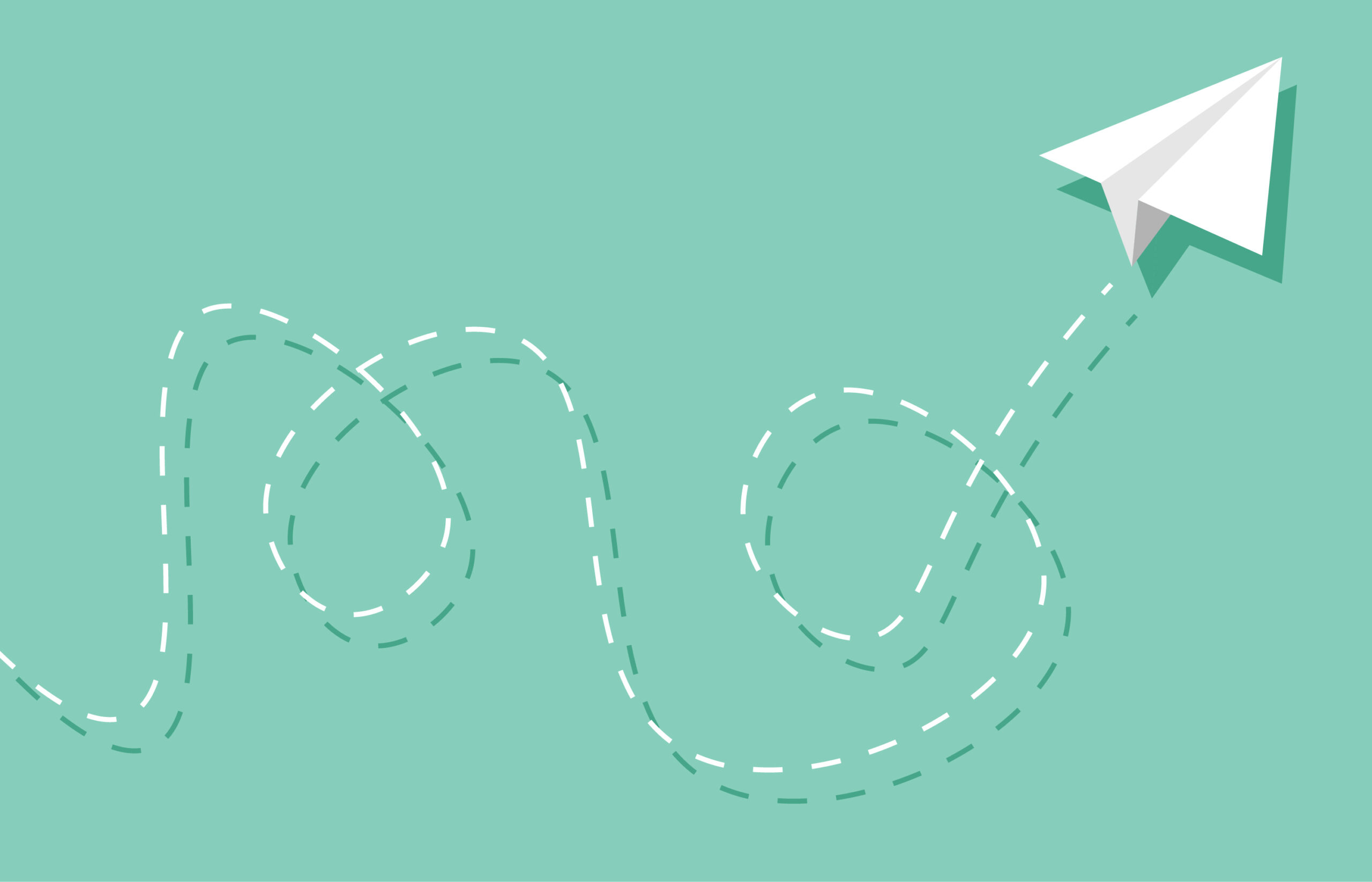
Visual Media’s Role in Marketing Your Risk Management Program
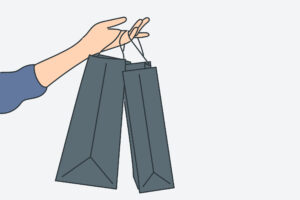
5 Risk Management Issues to Avoid During Peak Retail Season
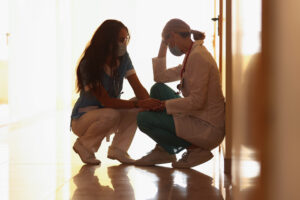
Keeping Clinicians Safe When Responding to Combative Patients
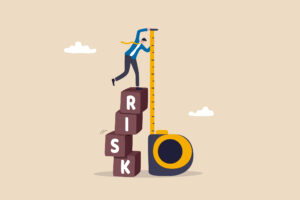
Why Your RMIS Dashboard Data Should Include Leading Indicators
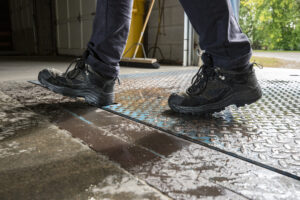
New Law Provides Additional Protections for Pregnant Workers
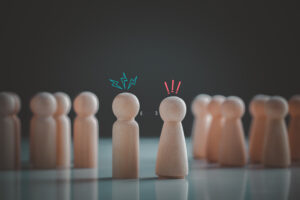
Using Anger Management Strategies to Reduce Workplace Violence
Environmental Health & Safety Office of Research Regulatory Support
Preventing slips, trips, and falls.
There are various ways to suffer slips and falls while working. You can slip and lose your balance, you can trip over objects left improperly left in your walkway, or you can simply fall from an elevated position above the ground. The following are some ways to help minimize slips, trips and falls in your work area. Contact the Occupational Safety Team at EHS for additional assistance or questions specific to your area.
Housekeeping
- Remove all trash, scrap materials, unused materials.
- Keep aisles, exits, and stairs free from materials, pallets, tools, fixtures, or other obstructions.
- Make regular housekeeping a priority. Keep areas clean and orderly so that buildup of trash or materials does not occur in the first place.
Maintenance
- Repair any holes, cracks, or uneven surfaces in the floor that could be a trip hazard.
- Select slip resistant floor coverings for areas that are a slip hazard. Keep floor mats at entry doors to allow for complete wiping of shoes.
- Use Caution Wet Floor signs when working in an area with a wet floor to notify others of the hazard.
- Use handrails. They are there to protect you should a fall occur. If you are carrying a load that impairs your ability to properly use the stairs, use the elevator or find someone to help you.
- Keep stairways in good repair and well lit.
- Never run on stairs
Be aware of your surroundings
- Beware of tripping hazards. Do not leave extension cords, tools, carts, or other items in walkways. If you see these items in walkways, pick up the items, or report the problem to a supervisor.
- Be on the lookout for slip hazards, such as water, grease, oil, food, sawdust, or other debris. Even a small amount is enough to make you fall.
- Walk where you are supposed to walk. Do not take short cuts through areas that are not to be used as walkways.
- Wear work shoes with non-skid soles and rubber heels.
- Be sure to thoroughly clean your shoes when entering a building in rainy or snowy weather.
Preventing falls from higher up
- Always use 3 points of contact when climbing a ladder, scaffold, or other equipment. Never overreach when using a ladder or other elevated equipment.
- Never jump from work platforms, loading docks, trucks, or other equipment.
Slips and Falls
Jump to navigation

For medical, fire or law enforcement assistance, call 911 For EH&S emergencies, including after hours, call (650) 725-9999
- Report a Safety Concern
- Staff Directory
Slip, Trip, Fall Inspection Form
This sample inspection form helps building and zone managers identify and eliminate slip, trip, and fall hazards found in common/shared areas. Conduct inspections for slip, trip, and fall hazards:
- At least annually, ideally prior to the wet season
- Before, during, and/or after construction and renovation activities, in situations where building occupants and the general public may be affected
For high-risk areas, perform a formal inspection at least on a quarterly basis, and more frequently depending on the likelihood for changing conditions. For common areas within the building, the building manager must conduct inspections.
During the inspection, evaluate of the following (at the very minimum):
- Condition of floors, carpets, and steps
- Floor maintenance protocol
- Housekeeping practices
- Lighting levels
- Presence and condition of guardrails/handrails at elevated work surfaces. Refer to Design Guidelines for specific requirements.

- Maps & Directions
- Search Stanford
- Terms of Use
- Emergency Info
© Stanford University , Stanford , California 94305 . Copyright Complaints

IMAGES
VIDEO
COMMENTS
1. Introduction. Falls on the same level are among the leading causes of accidental injuries and fatalities across many workplaces. Such falls, many subsequent to slips and trips, were ranked as the second most frequent cause of disabling workplace injuries after overexertion—accounting for 19.2 % of these injuries and imposing direct costs of $11.2 billion in the USA (Liberty Mutual, 2018).
Slips, trips and falls are responsible for the majority of general industry accidents and a leading cause of workers' compensation claims. Table 1 features related incident data on slips, trips and falls in private industry and public entities. Table 1: Event or exposure leading to injury or illness (incident rate 1), U.S. Bureau of Labor ...
Occupational slips, trips and falls on the same level (STFL) are a serious problem, with substantial injury and economic consequences reported worldwide. ... Citation 2005b, Citation 2005c), showed that lower limb strength could be a critical factor in trip recovery observed in laboratory situations, thus strength training might help reduce ...
Slips, trips and falls can happen in any workplace. They can occur at the entry of a building, in the kitchen, in cold rooms, on loading docks and even as you walk outside the building. More serious slips or trips together with the resulting falls may result in: • sprains or strains • broken bones when trying to break the fall
And you may not think so, but laboratory facilities are prime candidates for slips and falls. The constantly wet surfaces, frequent spills and splashes, constant washing of glassware, etc., all combine to make laboratories some of the places most vulnerable to slips, trips, and falls.
Slip, Trip, and Fall Prevention for Healthcare Workers. According to the U.S. Bureau of Labor Statistics [2009], the incidence rate of lost-workday injuries from slips, trips, and falls (STFs) on the same level in hospitals was 38.2 per 10,000 employees, which was 90% greater than the average rate for all other private industries combined (20.1 ...
Falls are when you lose contact with the walking or working surface and fall. Falls can occur either on the same level or from an elevated surface. Falls from an elevated surface are second only to motor vehicle accidents in the cause of work place fatalities. The hazards which result in slips, trips and falls generally can be grouped into ...
To minimize injury or death from incidents involving slips, trips, and falls, Stanford has developed prevention procedures, including worksite evaluations, hazard elimination, and employee training. The objectives of these procedures are to: Identify working environments where slip, trip, and fall hazards are most likely to occur.
The steps varied in height, causing the person to trip and fall, resulting in an ankle sprain and arm injury. On March 13, 2023, a person was ascending the steps at the entry of Bldg. 70A. Their trailing foot caught the edge of the top step, causing them to fall forward. The fall led to their shoulder impacting a glass door, which broke.
In June, safety trainings will cover slip, trip and fall prevention at Sanford Underground Research Facility (Sanford Lab). "Slips, trips and falls are a primary cause of work-related injuries," said Larry Jaudon, director of Sanford Lab's Environment, Safety and Health Department. "At Sanford Underground Research Facility, we take a ...
Importance. Slips, trips, and falls are common workplace accidents that can lead to injuries and financial losses for businesses. Most commonly, this training aims to protect lives and comply with safety regulations such as the Occupational Safety and Health Administration ().Proper safety training helps organizations identify and prevent hazards, which protects both of its employees and helps ...
This is an excerpt from our free guide on preventing slips, trips and falls.. A 2014 survey of 1,294 safety professionals revealed the most frequent factors in slip, trip and fall incidents at their workplaces—and a whopping 95% of respondents cited one of three causes.. The main characteristic the three biggest causes have in common is they're the result of the errors or errors in ...
How do falls happen? Statistics show that the majority (67%) of falls happen on the same level resulting from slips. and trips. The remaining 30% are falls from a height. This document will summarize. information on "falls on the same level" (slips and trips). Falls from an elevation, such as falls
Slips, trips and falls are the 2nd leading cause of accidental death (behind motor vehicle accidents). Over 17% of all disabling occupational injuries that occur in the U.S. result from falls Factors, such as the ones listed below, all contribute to an increased risk of slip, trip and fall injury.
NIOSH has looked into the value of wearing slip-resistant shoes. Laboratory studies of slip-resistant footwear to reduce slips, trips, and falls had shown promise in reducing slips, but until a few years ago, there was little research showing the effectiveness of slip-resistant shoes.
Call: 0818 289 389. Information on the causes of slips, trips and falls and practical precautions to prevent further slips, trips and falls from the HSA.
Slip is as long as 8-10 cm, resulting in instinctive efforts to regain postural control. Slide is uncontrolled movement of the heel typically when slip is greater than 10 cm. Likely to lead to a loss of balance and result in a fall. Trip occurs when the swing phase of the foot is interrupted unexpectedly due to inadequately clearing the ground.
Preventing Slips, Trips, and Falls. There are various ways to suffer slips and falls while working. You can slip and lose your balance, you can trip over objects left improperly left in your walkway, or you can simply fall from an elevated position above the ground. The following are some ways to help minimize slips, trips and falls in your ...
Slip, Trip and Fall Prevention. Slips, trips and falls are the second leading cause of injury in the workplace and result in approximately 25,000 accidents daily in the United States, according to the National Safety Council. Many factors contribute to slips, trips and falls. While these types of injuries are commonplace, Travelers Risk Control ...
Slips, trips, and falls happen often. In fact, 27.4% of nonfatal workplace injuries in private industry were caused by slips, trips, and falls. If we look at the big data, in 2019 in the United States, there were 888,220 workplace injuries (reported), and 244,000 were slips, trips, and falls caused.
Understand what causes slips and trips and how to prevent them. Your role: employers, workers, designers. Find out what you can do in your role to prevent slips and trips. Case studies. Get examples of how others have solved common problems. Resources. Publications, tools, research. Subscribe.
This sample inspection form helps building and zone managers identify and eliminate slip, trip, and fall hazards found in common/shared areas. Conduct inspections for slip, trip, and fall hazards: For high-risk areas, perform a formal inspection at least on a quarterly basis, and more frequently depending on the likelihood for changing conditions.